What is Porosity in Welding: Important Tips for Getting Flawless Welds
What is Porosity in Welding: Important Tips for Getting Flawless Welds
Blog Article
The Scientific Research Behind Porosity: A Comprehensive Overview for Welders and Fabricators
Comprehending the detailed systems behind porosity in welding is vital for welders and producers aiming for impressive craftsmanship. From the composition of the base materials to the complexities of the welding procedure itself, a multitude of variables conspire to either exacerbate or ease the visibility of porosity.
Comprehending Porosity in Welding
FIRST SENTENCE:
Evaluation of porosity in welding reveals crucial insights into the stability and top quality of the weld joint. Porosity, characterized by the visibility of cavities or spaces within the weld metal, is a typical concern in welding processes. These spaces, if not properly attended to, can compromise the architectural stability and mechanical buildings of the weld, leading to potential failings in the completed product.
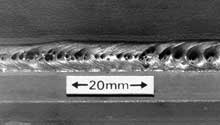
To find and quantify porosity, non-destructive screening approaches such as ultrasonic screening or X-ray evaluation are typically utilized. These strategies enable the identification of inner flaws without compromising the stability of the weld. By examining the size, form, and circulation of porosity within a weld, welders can make informed decisions to boost their welding procedures and achieve sounder weld joints.
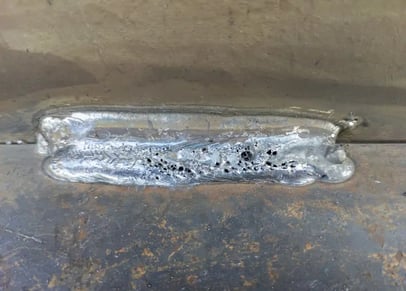
Elements Affecting Porosity Formation
The event of porosity in welding is affected by a myriad of aspects, varying from gas shielding efficiency to the ins and outs of welding parameter settings. Welding specifications, including voltage, current, take a trip speed, and electrode type, additionally effect porosity formation. The welding strategy used, such as gas steel arc welding (GMAW) or protected steel arc welding (SMAW), can influence porosity formation due to variations in heat circulation and gas coverage - What is Porosity.
Effects of Porosity on Weld High Quality
Porosity development significantly endangers the architectural honesty and mechanical homes of bonded joints. When porosity exists in a weld, it develops spaces or dental caries within the material, reducing the total toughness of the joint. These spaces function as stress focus points, making the weld a lot more susceptible to fracturing and failing under tons. The existence of porosity likewise weakens the weld's resistance to deterioration, as the caught air or gases within the gaps can respond with the surrounding setting, resulting in deterioration with time. Additionally, porosity can impede the weld's capacity to stand up to stress or impact, more threatening the general quality and reliability of the bonded index framework. In vital applications such as aerospace, vehicle, or structural buildings, where security and longevity are paramount, the damaging impacts of porosity on weld top quality can have extreme repercussions, emphasizing the value of decreasing porosity via correct welding methods and procedures.
Strategies to Minimize Porosity
To enhance the top quality of bonded joints and make sure structural stability, welders and fabricators employ specific strategies focused on decreasing the development of voids and tooth cavities within the product throughout the welding procedure. One reliable method to minimize porosity is to make sure appropriate material preparation. This consists of extensive cleansing of the base metal to get rid of any pollutants such as oil, grease, or dampness that could contribute to porosity development. In addition, utilizing the appropriate welding specifications, such as the appropriate voltage, existing, and travel speed, is essential in avoiding porosity. Maintaining a constant arc size and angle during welding also aids lower the possibility of porosity.

In addition, picking the ideal securing gas and keeping appropriate gas flow prices are necessary in decreasing porosity. Using the suitable welding strategy, such as back-stepping or utilizing a weaving you can try this out activity, can likewise assist disperse warm evenly and decrease the chances of porosity development. Lastly, making certain proper ventilation in the welding setting to eliminate any type of possible resources of contamination is important for achieving porosity-free welds. By implementing these methods, welders can effectively decrease porosity and generate top notch bonded joints.
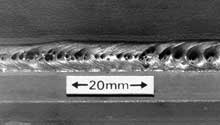
Advanced Solutions for Porosity Control
Executing advanced innovations and innovative techniques plays a critical function in achieving superior control over porosity in welding procedures. One innovative solution is using advanced gas blends. Protecting gases like helium or a blend of argon and hydrogen can help in reducing porosity by offering better arc security and improved gas protection. Additionally, utilizing advanced welding methods such as pulsed MIG welding or customized ambience welding can likewise aid mitigate porosity issues.
Another innovative solution entails the use of innovative welding devices. Utilizing tools with built-in features like waveform control and innovative power resources can boost weld top quality and decrease porosity dangers. The implementation of automated welding systems with precise control over parameters can dramatically lessen porosity defects.
Furthermore, incorporating innovative monitoring and examination innovations such as real-time X-ray imaging or automated ultrasonic screening can assist in detecting porosity early in the welding process, Continue allowing for prompt corrective actions. Generally, integrating these innovative options can greatly improve porosity control and improve the total quality of welded elements.
Verdict
Finally, understanding the science behind porosity in welding is vital for welders and makers to generate top quality welds. By determining the factors affecting porosity formation and implementing strategies to reduce it, welders can improve the total weld top quality. Advanced services for porosity control can even more improve the welding process and guarantee a strong and reliable weld. It is essential for welders to continually educate themselves on porosity and carry out ideal methods to attain optimum outcomes.
Report this page